Ultrafine processing technology continues its evolution
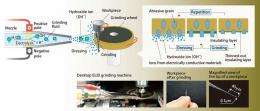
The performance of optical and electronic components such as lenses and semiconductors is strongly influenced by the precision of surface grinding, which involves shaping the surface, and polishing, and provides the product with a mirror finish. Electrolytic in-process dressing (ELID), a technological innovation developed more than 20 years ago by Hitoshi Ohmori, chief scientist of the Materials Fabrication Laboratory at the RIKEN Advanced Science Institute, revolutionized these processes by providing nanometer-level precision in surface finishing. Ohmori’s laboratory frequently plays host to researchers and industry engineers interested in new methods, and his group continues to make steady improvements to the ELID grinding technology. Now, the laboratory has its sights set on a new target—what Ohmori calls “broadband fabrication.”
A work in progress
In 1987, almost a quarter of a century ago, Ohmori published a paper on the electrolytic in-process dressing (ELID) grinding method. At that time, mirror finishing required two separate processes: grinding and polishing. ELID made it possible to perform the two simultaneously.
“An ELID grinding wheel is a uniform mixture of electrically conductive materials including metals and abrasive particles such as pieces of diamond,” says Ohmori. “A conventional grinding wheel rotates to grind the workpiece with a relatively high degree of precision, but frequently becomes clogged or glazed after a short period in use, meaning that the grinding work must be stopped to ‘dress’ or sharpen the grinding wheel in order to make abrasive grains protrude from the wheel surface. In contrast, ELID enables grinding with in-process dressing because electrically conductive (mainly metallic) bonding materials on the grinding wheel are selectively removed by electrolytic action while the surface of the workpiece is being ground with extreme precision. As the degree of dressing can be controlled electrically, ELID allows very fine abrasive grains to be used, making it possible to reduce the size of grinding traces and making precision mirror-quality finishing a reality.”
ELID attracted broad interest in industry because of its innovativeness. Later, with demands for higher work surface precision increasing day-by-day and a growing range of soft work materials in use, such as special metals or composite materials, further development of the ELID method became paramount. For some time, smaller abrasive grains were used to process these pieces. However, using abrasive grains smaller than 1 micrometer with such rigid bonding materials as metals led inevitably to vibration problems, placing limitations on the ground surface precision due to a lack of grinding wheel rotational precision. This made technological innovation essential.
In 1993, Ohmori started working on ELID using an ‘elastic’ grinding wheel and successfully developed a system capable of creating a mirror-finish surface with an average roughness of just 0.3 nanometers. “Despite what the word ‘elastic’ might suggest, metal accounts for 60–70% of the grinding wheel, with the rest made up of synthetic resin or plastic. The ratio is just right. Today, elastic grinding wheel-based ELID has become the mainstream, and is commonly used for finishing optical components such as mirrors.”
Ohmori subsequently started working on machining three-dimensional shapes. He combined ELID with machine tools capable of positioning the grinding wheel and workpiece with a resolution of 1 nanometer or less, successfully developing a computerized, superfine, multi-degree-of-freedom machining system to mirror-finish aspheric lenses.
Today, there is a growing need for microfabrication, which allows more efficient machining and production of fine components with a higher degree of accuracy than previous machines. Figure 1 shows a desktop ELID grinding system that can produce a working tip diameter of 1 micrometer or less. The tip functions as a tool, sensor and electrode. Out of a conviction that small grinding machines could be developed for small workpieces, in 2004 Ohmori created a desktop ELID grinding machine with electrodes built into the nozzle that sprays grinding fluid. The grinding machine can process workpieces like the long tapered micro-tool shown in Fig. 1 without breakage and to nanometer-surface precision. To make the system even more compact, a smaller electrolytic power-generating unit for the desktop ELID grinding machine was developed in 2010.
Desktop ELID grinding machines can now be found in many companies, research institutes, and universities. “The machine allows precision machining of small workpieces of 1 micrometer to 10 centimeters in size. It also has a small footprint and runs on commercial AC 100V power. It is generally used to process small numbers of workpieces. We envision that mass-produced items will be manufactured in large-scale factories to reduce production costs, while the desktop ELID system is suitable for on-demand fabrication and precision machining in relatively small quantities,” says Ohmori.
The major users of ELID are manufacturers requiring precision machining. They manufacture a wide range of items ranging from optical components, semiconductors, dies and molds and automobiles to medical components. Some manufacturers have customized the ELID grinding machine and introduced it onto their mass- production lines. In 2006, Ohmori developed the ELID honing method in partnership with Fuji Heavy Industries by applying ELID to the honing process for finishing the cylinder inner walls in automobile engines, successfully reducing the processing time by half.
Rubber and carbon grinding wheels
ELID continues to evolve. One of the current research themes Ohmori and his laboratory members are working on is the development of a new grinding wheel that is even more elastic than previous models. One of the candidate materials is rubber. Pure rubber, however, cannot be electrolyzed because it does not conduct electricity. “We are planning to develop a grinding wheel made of a mixture of rubber and electrically conductive materials or metals,” says Ohmori. Carbon is one of the candidates.
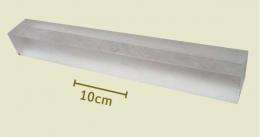
One application for ELID using a carbon-containing elastic grinding wheel is in the machining of the backside surfaces of memory substrates. With ELID, the silicon substrates can be made thinner and subsurface damage by grinding can be minimized. The ELID method, however, leads to the production of metal ions from the grinding wheel through electrolysis. “In most cases, this was not a major problem. However, manufacturers asked us to develop an ELID grinding wheel without any metals, so we came up with the idea of using carbon. We used carbon because it is not a metal, but still conducts electricity and does not affect semiconductors when ionized.”
The laboratory is planning to produce the carbon material for the grinding wheels itself. “We will use untapped natural resources such as rice bran or waterweeds such as reeds. When waterweeds are burned they leave behind fibrous carbon. We are still at the basic research stage, but our carbon grinding wheel may exhibit unique characteristics.” In the future, they may be able to put environmentally friendly grinding wheels with carbon produced from rice bran or waterweeds into practical use.
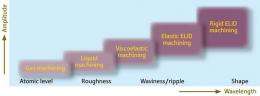
Changing surface properties
The second research subject of the Materials Fabrication Laboratory is surface modification. When ELID first appeared, users sometimes noted that a surface finished using ELID became rust-resistant. “We were surprised at this unexpected feedback. We examined the mechanism and found that the key was hydroxide ions (OH–). Electrolysis causes the grinding fluid to produce OH– while it is flowing from the electrodes to the grinding wheel. The hydroxide ions falling onto the surface of the grinding wheel dress the wheel, and they also fall on the surface of the workpiece, forming a thin oxidized layer that serves as a protective, rust-resistant film. ELID is therefore very suitable for machining rust-susceptible mold materials and various medical products such as dental implants and artificial joints.
Ohmori is now looking at ways to use the surface modification characteristics more actively. Intentional modification of the components of the abrasive grains or grinding fluid can lead to the generation of a variety of surface modification characteristics. “For example, changing diamond-based abrasive grains to aluminum- or chromium oxide-based grains can contribute to changes in the wettability of the surface. When the surface of a workpiece is machined with a grinding wheel containing abrasive grains made up of a mixture of diamond and silica, it exhibits good adhesion with a coating layer applied later. We also found that the workpiece became stronger.”
The surface modification functionality of ELID is also what makes it possible to machine long tapered micro-tools such as that shown in Fig. 1 without breakage. “Investigation showed that many oxygen ions penetrated the inside of the workpiece during machining, strengthening its metal structural bonding forces.”
Overall, the ELID grinding method has three distinct advantages over other machining techniques: it is suitable for processing complex shapes such as combined curved surfaces, it can be used to machine a smooth mirror finish to a surface precision of 1 nanometer, and it adds functionality to the surface of the workpiece. “Recently, our research has been shifting towards adding functionality.”
From finishing to broadband fabrication
“The ELID grinding method has seen major improvements, from a rigid grinding wheel to an elastic grinding wheel. The next target is liquid tool machining instead of solid tool machining,” says Ohmori.
In 2008, in collaboration with Kazuto Yamauchi of Osaka University, Ohmori developed a light-collecting mirror (Fig. 2) for X-ray light produced by the SPring-8 Angstrom Compact Free Electron Laser (SACLA) at the RIKEN Harima Institute, which was completed in March 2011. The light-collecting mirror has a complex aspheric surface. Surface precision at the atomic level was required for the mirror finish. “Even ELID was insufficient for finishing the surface to that level of precision. We attempted to combine ELID grinding with elastic emission machining (EEM), which has been studied by the research group headed by Prof. Yamauchi. EEM uses a chemical reaction and provides mirror-finish machining at the single atom level. We first used ELID to produce the shape with the specific surface precision of the mirror, and then used EEM to finish the mirror to the single-atom level. Nobody else has developed the technology for completing long aspheric surfaces to that level of precision.”
The light-collecting mirror was developed by Ohmori and Yamauchi by combining their two machining methods. At present, Ohmori is studying a new finishing method that will make a foray into uncharted territory. “Liquid-tool machining allows mirror finishing to single-atom precision, but it takes an enormous amount of time to finish workpieces with large, uneven surfaces. So we are working on finding a way to shorten the machining time and improve the machining precision by using more viscous liquids or viscoelastic bodies.” Candidate viscoelastic bodies include fluids that increase in viscosity when a magnetic field is applied and return to free liquid form when the magnetic field is removed. Changing the strength of the magnetic field can be used to control the viscosity. “To begin with, the surface of the workpiece is planarized with the solid-tool machining principle. Then magnetic viscous fluids (acting as a semi-liquid-tool) are applied to the surface to smooth any unevenness remaining on the pre-machined surface. Finally, liquid-tool machining is applied to finish the surface to the single-atom level of precision.”
“We are studying how to apply gas polishing (gas-tool machining), which is a process to remove processing strain and/or subsurface damages by applying gas plasma to the surface of the pre-finished workpiece. We are planning to develop a prototype product later this year,” says Ohmori. With this technique, ionized gas particles are applied to the surface of the workpiece in the same way as plasma etching in a vacuum.
Ohmori has devised and developed new methods one after another. “Our goal, however, is to make broadband fabrication technology a reality,” he says. “When the cross-section of a workpiece is regarded as a wave, we can see that the overall shape, large curves, and rough irregularities are nested like a waveform. Depending upon the wavelength and amplitude of the surface, rigid, elastic, viscoelastic, liquid and gas-tool machining each have their own area of proficiency. In order to finish a workpiece in a finite period of time to within a prescribed precision irrespective of the type of target workpiece, it is best if all adjacent machining regions overlap to produce a ‘broadband’ machining region. We will face many research challenges in these overlapping regions, such as clarification of the machining mechanisms and development of controlling and tuning technology. However, we hope to establish a new methodology and a new field: broadband fabrication. When we have transformed machining principles to include broadband, we will be able to get a clear view of the most suitable machining principle and method, or the best combination of machining principles and methods, for any required size and precision.
Supporting cutting-edge science and technology
Recently, researchers have been making an increasing number of requests not only for ELID and microfabrication, but also for ‘ultrafabrication’, which deals with large target workpieces. “Machining large objects requires significant time. The objects expand or contract with changes in temperature, causing tool wear or misalignment of the machining position. No precision measuring instruments have been developed to work on large pieces. We also need specific programs to ensure stable machining precision. Thus, ultrafabrication has to be applied on an individual product basis.”
One example of an ultrafabrication-based product is the lens for the JEM-EUSO telescope that will be installed in the Japanese Experimental Module (JEM) ‘Kibo’ laboratory in the International Space Station (ISS). The acrylic lens is 1.5 meters in diameter. Fresnel processing was required to cut shallow and sharp grooves on both sides as well as thinning to produce a lightweight diffractive lens. Machining the large sunlight collection lenses is an example of ultimate ultrafabrication. A two-meter lens has already been requested for research and development purposes to explore new applications that include laser beam and energy generation using solar energy collectors.
Other requests include lenses for astronomical observation equipment and cutting-edge research in optical science. “The requirements for cutting-edge optical devices will continue to increase in the future. To meet these requirements, we need to make broadband fabrication technology a reality.”
When a new requirement becomes apparent, Ohmori makes it a rule to set the machining guidelines from three perspectives. The first is the size of the workpiece, where ultrafabrication and microfabrication are the two extremes. The second is quantity, which extends from single-product machining to mass-production. “The key is to have a viewpoint of on-demand fabrication that enables flexible and quick production in response to various needs,” says Ohmori. The third perspective is precision, with the guideline that machining should aim for precision of one nanometer.
“Looking back over the last 20 years since the publication of my paper on the ELID grinding method, I regret that I seem to have responded on a case- by-case basis. I think I could have made more progress if I had seen the individual improvements as being technically linked to each other and if I had worked on them at the same time. In the future, I will continue to systematize the various techniques we have built up, including newly developed techniques such as broadband fabrication technology, so that we can deal rationally with various external requirements by analyzing them from these three viewpoints or by selecting suitable tools and approaches accurately and promptly.”
Ohmori is now searching for a way to help Japan’s skilled manufacturing survive in an increasingly competitive global economy. He is also working on innovative technologies that support cutting-edge science and technology. “Our dream is to use our technology to help researchers win the Nobel Prize.”
Provided by RIKEN